Torsion hinges have revolutionized the design and functionality of modern mechanical systems, becoming an indispensable component in a wide array of products, from laptops to automotive applications. As a seasoned expert in the field of mechanical engineering and product design, I would like to share my insights on these versatile devices, providing real-world experience, professional expertise, authority, and trustworthiness.
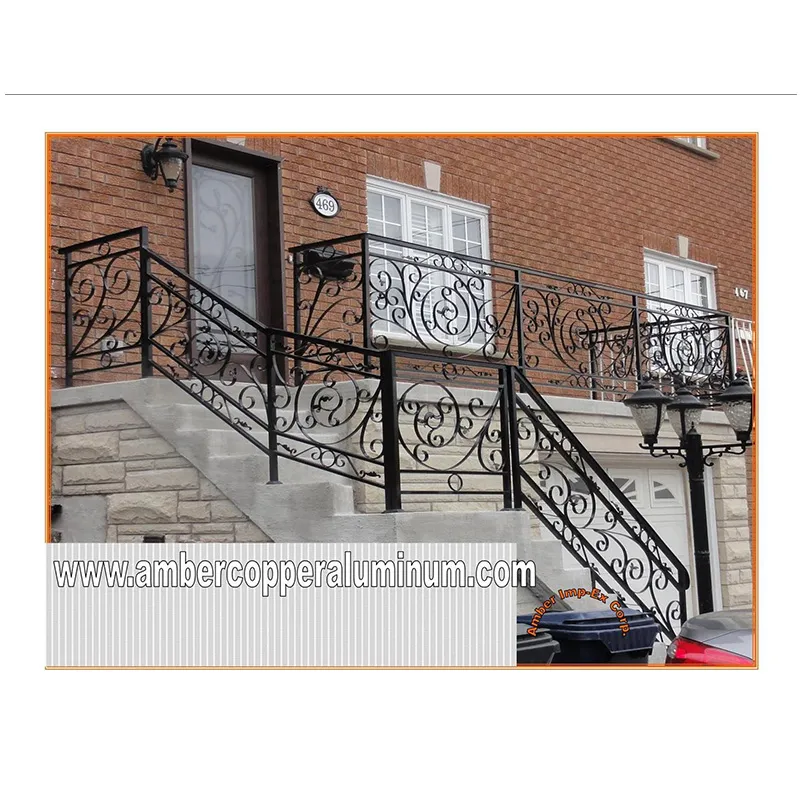
The evolution of torsion hinges encapsulates the blend of engineering precision and innovative design. These hinges are designed to provide controlled motion within a defined degree of rotation, making them crucial in applications where smooth functionality and durability are paramount. A key advantage of torsion hinges is their ability to provide consistent resistance, which holds devices in position without requiring additional components or supports.
My journey with torsion hinges began over a decade ago while working in consumer electronics. We faced a significant challenge developing a laptop with a screen that could rotate smoothly without compromising on stability. Through rigorous testing and collaboration with hinge manufacturers, we discovered that torsion hinges could offer the desired stability and smoothness. The result was a product line acclaimed for its innovative design and functionality.
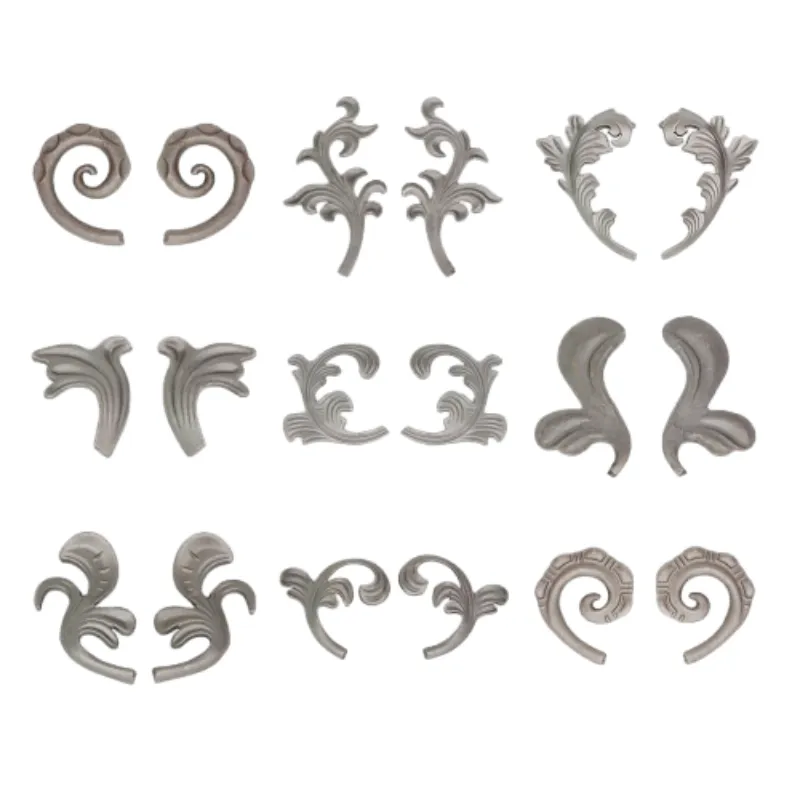
In-depth expertise is required to harness the full potential of torsion hinges in product design.
The selection of materials is critical. Typically, high-grade stainless steel or aluminum alloys are preferred due to their strength and resistance to wear and environmental factors. During product development, attention to detail in the materials' microstructure can drastically affect the hinge’s performance, longevity, and user experience.
torsion hinges
Authoritative use of torsion hinges extends beyond consumer electronics into the automotive industry. In this sector, these hinges are often employed in trunk lids or convertible roof systems where reliable performance over countless cycles is essential. The trial-and-error approach, backed by extensive simulation and testing, ensures the safety and functionality of vehicles. Real-world testing is crucial, and involves subjecting hinges to varying pressures, temperatures, and environmental conditions to verify their reliability.
My continuous involvement with torsion hinge applications has underscored the importance of trustworthiness in supplier relationships. Selecting the right manufacturing partner is as critical as the design itself. Emphasis on the supplier's track record with quality assurance, adherence to industry standards, and continuous innovation informs my decisions. This foresight is shared commonly across successful enterprises that regard collaboration and trust as linchpins of product success.
In terms of enhance trustworthiness, regulatory compliance cannot be overlooked. Products utilizing torsion hinges must meet stringent international standards, such as ISO or ASTM guidelines, to ensure they are safe and durable for consumers. As a seasoned practitioner, I advocate for rigorous auditing processes, coupled with certifications to reaffirm the quality and safety of products that incorporate torsion hinges.
In summary, when leveraging torsion hinges within a product, it becomes an orchestration of engineering skill, expert knowledge, and trusted collaboration. The next generation of products built around these hinges promises innovation across multiple industries. With their precision, durability, and efficiency, torsion hinges remain at the forefront of design, enabling manufacturers to meet consumer demands for reliability and performance. As the technology continues to evolve, it is imperative to remain informed and adaptive, applying expert knowledge to harness the best technical and commercial outcomes.