U groove pulley wheels, integral components in numerous mechanical assemblies, offer diverse functionalities that enhance the efficiency of various systems. These pulley wheels, designed with a U-shaped groove, assist in guiding cables and belts within systems, ensuring precision and stability. The engineering and manufacturing communities recognize U groove pulley wheels for their ability to optimize performance in dynamic environments.
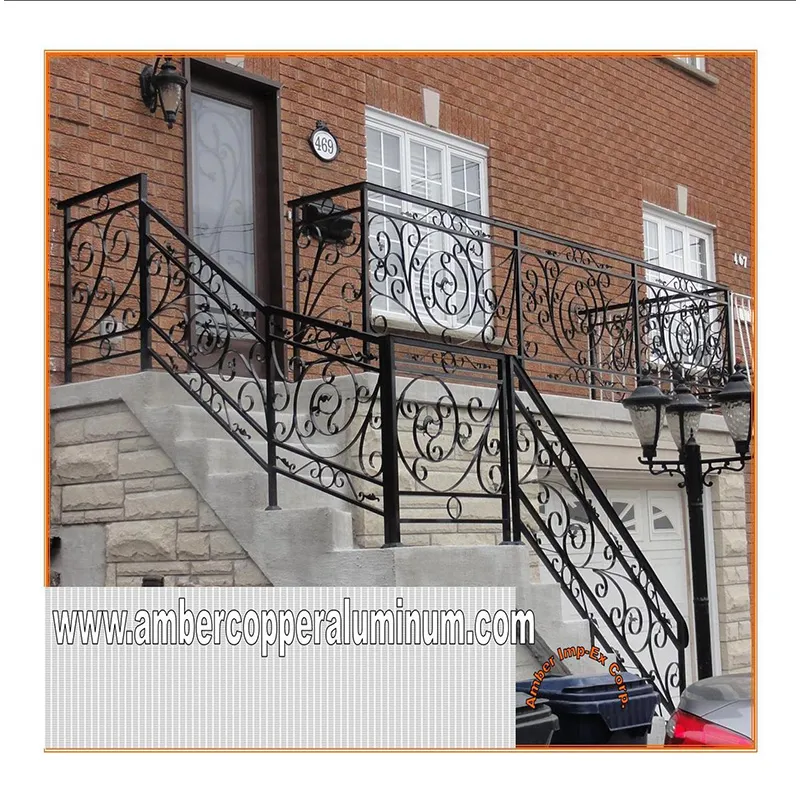
The design of U groove pulley wheels is focused on reducing friction and wear within operating systems. The U-shaped groove on the pulley's circumference accommodates cables tightly, preventing slippage and facilitating smooth motion. This characteristic makes them indispensable in settings requiring consistent tension and alignment, such as conveyor systems, automotive machinery, and production equipment.
In the context of real-world experiences, industries that prioritize operational efficacy often rely on U groove pulley wheels. An example can be seen in conveyor belt systems found in manufacturing plants. Here, the choice of pulley wheels can significantly impact the system’s reliability and longevity. U groove pulley wheels ensure that belts are kept securely in track, minimizing downtime caused by misalignment or belt slippage. Plant operators frequently attribute reduced maintenance needs and prolonged service life of equipment to the usage of these pulleys.
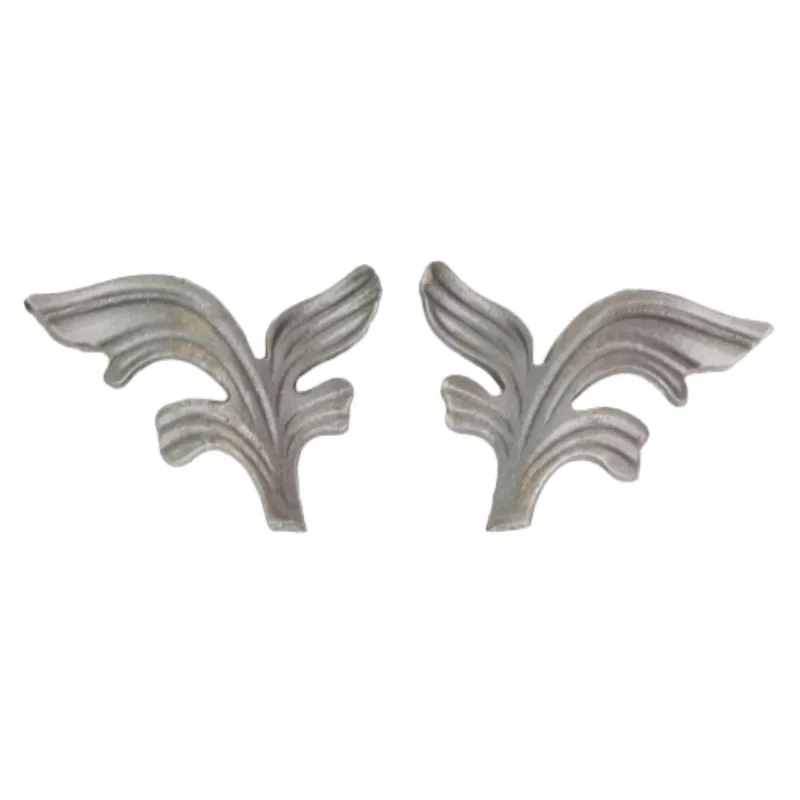
One hallmark of expertise in the realm of U groove pulleys is material selection. Practitioners understand that the choice of materials impacts load capacity, wear resistance, and thermal performance. Common materials like aluminum, steel, and plastic each offer unique benefits. Steel, with its superior durability, often finds applications in heavy-duty settings. However, when weight and corrosion resistance are paramount, aluminum becomes a preferred choice. Advanced composites and plastics are often selected for applications requiring reduced noise and enhanced corrosion resistance.
Authority in the domain of U groove pulley wheels is demonstrated through commitment to quality standards and certifications. Reputable manufacturers test these components rigorously for parameters like load bearing capacity, material stress limits, and durability under varying environmental conditions. By ensuring stringent compliance with these standards, these manufacturers affirm the dependability and safety of their pulleys in critical applications.
u groove pulley wheels
Trustworthiness in the selection and use of U groove pulley wheels stems from transparent sourcing and manufacturing processes, along with comprehensive product documentation. When engineers and designers select these pulleys, they rely on detailed specifications provided by manufacturers. This data enables accurate assessments of compatibility with existing systems and predicted performance outcomes. Additionally, user reviews and testimonials can offer valuable insights into the long-term reliability and performance of specific pulley models.
The advancement of technology continues to refine the utility of U groove pulley wheels, incorporating features like enhanced heat dissipation and noise reduction. Innovations such as self-lubricating properties and corrosion-resistant coatings are increasingly common, further expanding their usability across various industrial sectors.
In particular, robotics is an emerging field that heavily benefits from the precision and reliability of U groove pulley wheels. In robotic arms and automated systems, the pulleys ensure that cords and belts operate under optimal tension and alignment, critical for the accuracy and consistency required in automated tasks.
Ultimately, the effective integration of U groove pulley wheels into machinery and equipment underscores a blend of engineering precision and practical application. Their ability to enhance performance, reduce maintenance demands, and provide reliable operation makes them indispensable in modern mechanical design. As technology evolves, so too will the capabilities and applications of these versatile components, driven by the ongoing pursuit of efficiency and innovation in mechanical systems.