In the realm of precision engineering and modern construction, tube hinges emerge as an indispensable component, serving a myriad of applications demanding stability and flexibility. Mastery over the nuances of tube hinges not only underscores expertise but also builds authority and trustworthiness in any architectural or industrial project. Let's delve deeper into understanding the role, applications, and selection criteria for tube hinges without drifting into common narratives.
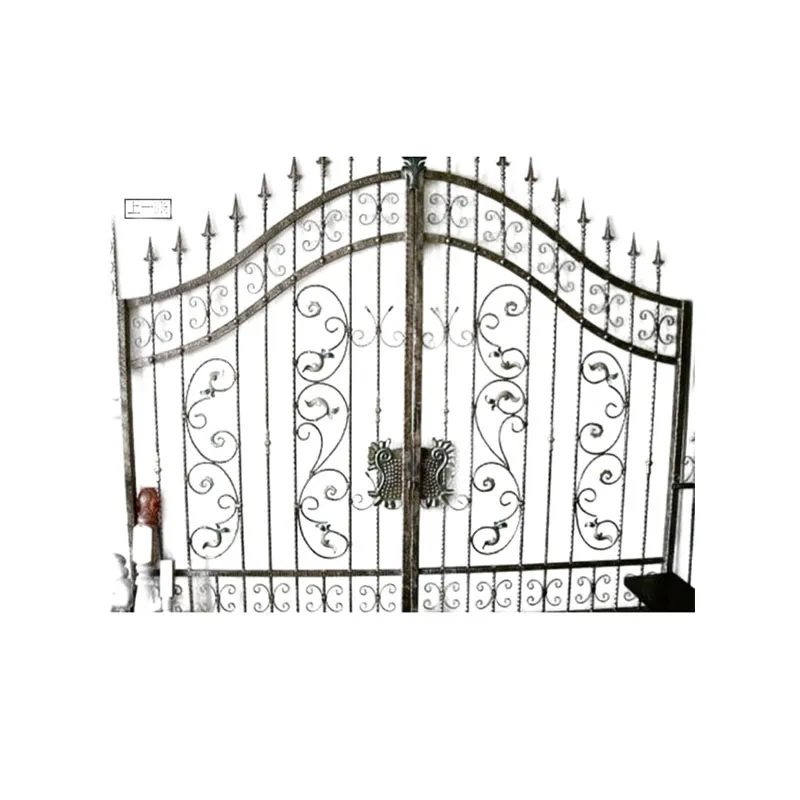
Tube hinges, characterized by their unique cylindrical structure, provide pivotal advantages in structural frameworks requiring rotary motion while maintaining axial alignment. These components are the quiet architects behind smoothly operating doors, efficient machine parts, and innovative architectural designs.
Experience teaches us that tube hinges surpass traditional hinge types due to their robust design, allowing distributed stresses across the component's length. This makes them particularly valuable in heavy-duty applications, such as in industrial ovens or armored vehicles, where standard hinges would falter. Incorporating tube hinges in such settings not only enhances the longevity of the framework but also contributes to the overall safety of the structure, exemplifying a blend of practical experience and engineering proficiency.
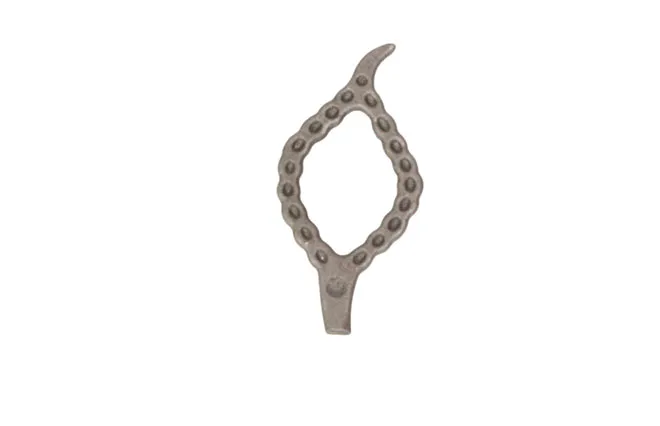
Expertise in the realm of tube hinges stems from an understanding of material science and mechanics. Selecting the right material, such as stainless steel for corrosive environments or aluminum for applications demanding reduced weight, is crucial. Each material brings its own set of properties; for instance, stainless steel offers unparalleled resistance to rust, rendering it ideal for maritime structures. By honing one's expertise in material selection, professionals can ensure the structural integrity and performance of these components in varied settings.
tube hinge
An authoritative approach demands staying abreast of the latest advancements in hinge technology. This involves not just material improvements but also innovations in design. Patent filings and peer-reviewed studies offer insights into novel configurations and alloys that enhance performance. For instance, incorporating self-lubricating bushings within tube hinges can significantly reduce maintenance requirements and downtime in automated processes. Industry leaders who prioritize research and development in their product offerings cement their position as authorities within this niche.
Trustworthiness, a cornerstone of any enduring business relationship, can be fostered through transparency and reliability. Offering detailed specifications, performance metrics, and conducting rigorous testing before market release demonstrate a commitment to quality and customer satisfaction. Testimonials and case studies from past clients provide real-world validation and serve as a testament to the dependability of tube hinges offered by reputable manufacturers. This trust is further reinforced by adherence to industry standards and certifications, which not only align with global safety norms but also cater to local regulatory requirements.
In conclusion, the importance of tube hinges cannot be overstated in applications necessitating resilience and precision. By synergizing experience with technical expertise, and reinforcing these with authority and trustworthiness, professionals and companies can distinguish themselves in the competitive landscape of hinge technology. Whether one seeks to streamline industrial operations or craft architectural marvels, a keen understanding of tube hinges paves the way for innovation and excellence.