Mastering Pulley Operations A Comprehensive Guide
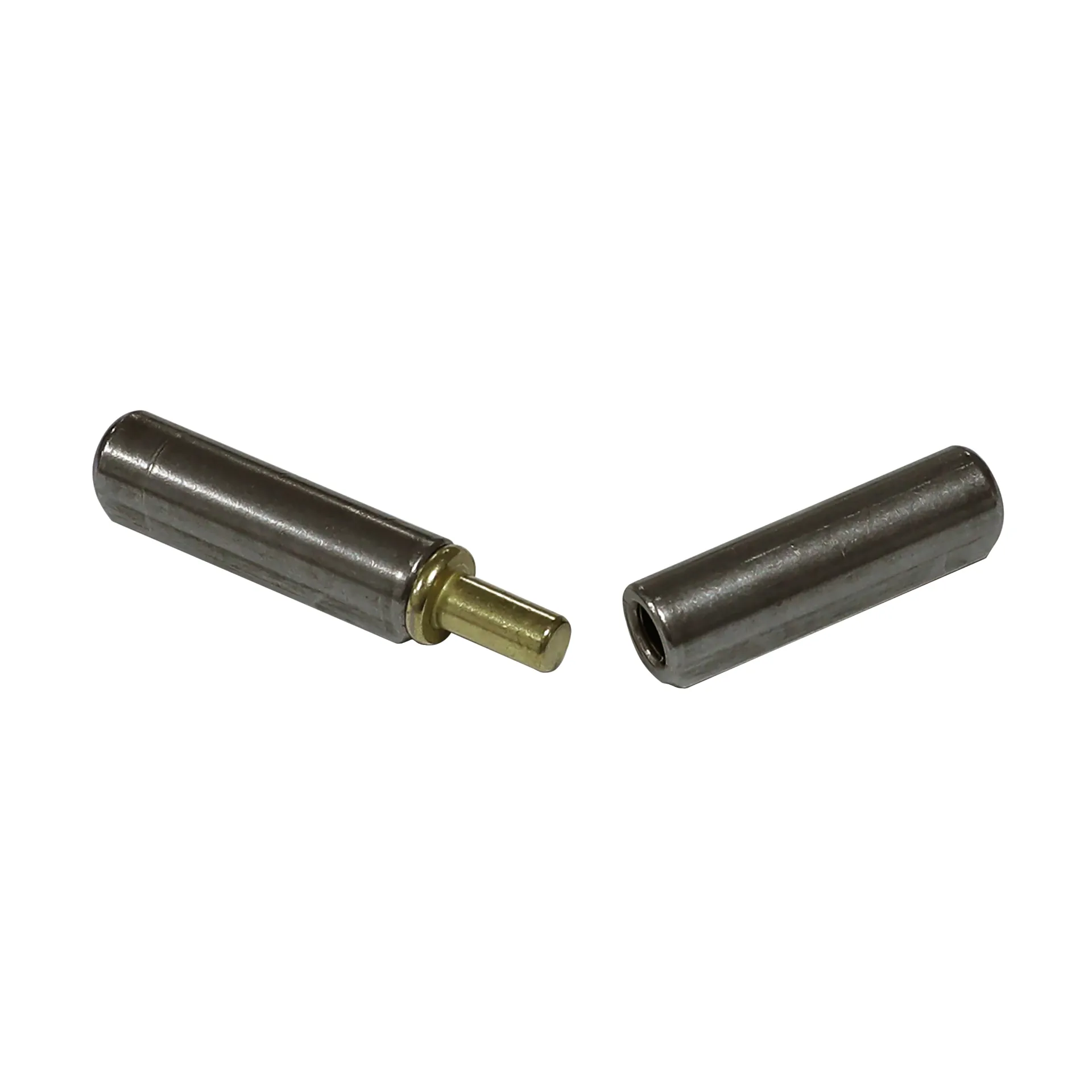
In the intricate world of industrial operations, pulleys have steadfastly remained a pinnacle of engineering utility. Whether you're pulling your first ropes or are a seasoned professional, understanding the nuances of pulley operations is essential for optimizing productivity while ensuring safety.
Pulleys, simple machines that are part of our rich engineering history, have evolved remarkably, maintaining their role in lifting and transporting loads. They are the backbone of many mechanical systems and integral to various sectors, ranging from logistics and manufacturing to maritime and aerospace. This guide aims to enhance your understanding of pulleys through expert insights and authoritative expertise, ensuring you gain a credible grasp of pulley operations.
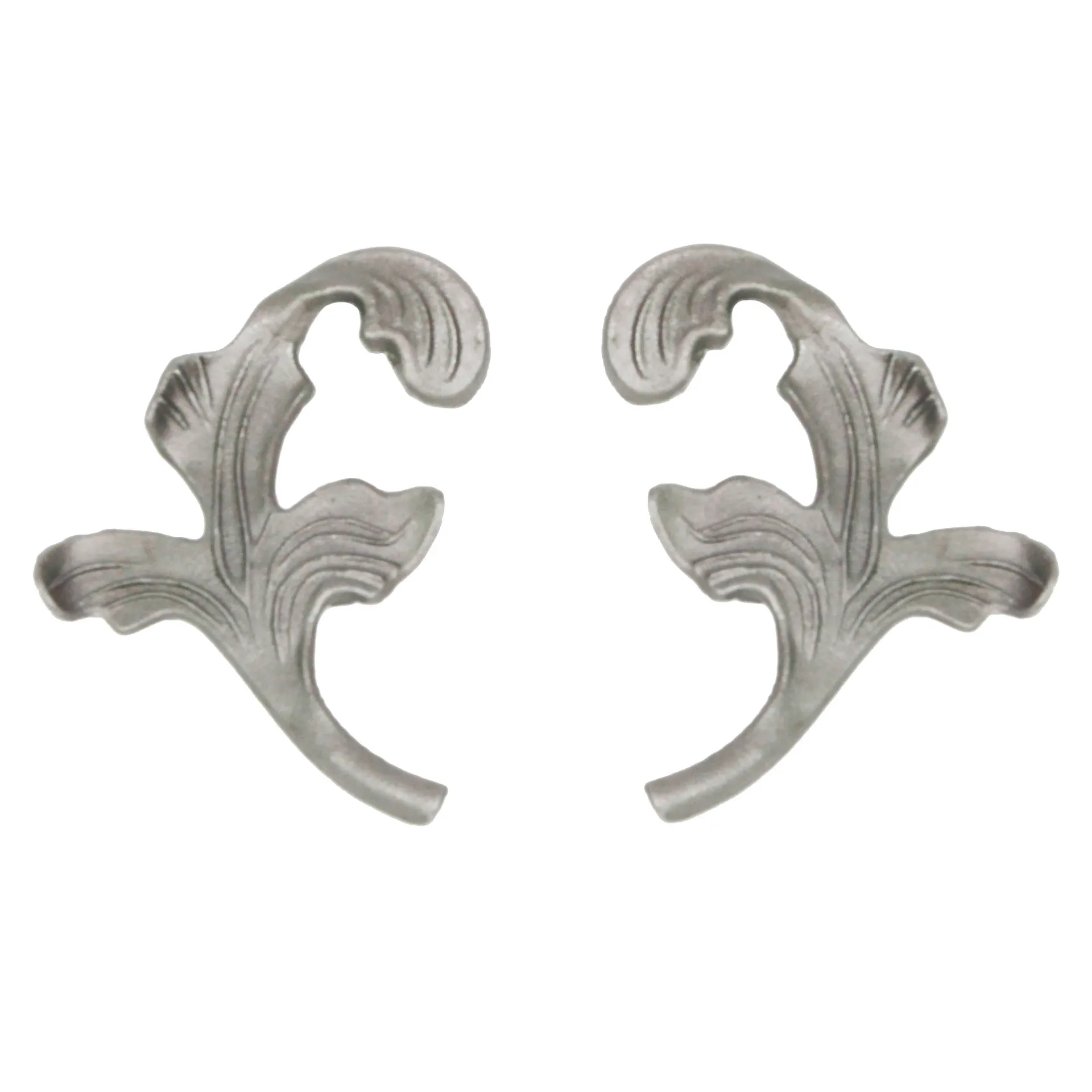
At the heart of pulley operations is the ability to reduce the amount of force needed to lift an object—this is achieved through changing the direction of force via the pulley’s wheel and axle mechanism. Experienced professionals know that selecting the right type of pulley system is vital to match the specific operational requirements. The three main types of pulleys—fixed, movable, and compound—offer varied mechanical advantages and must be chosen wisely.
The fixed pulley, despite its simplicity, is a marvel in scenarios requiring change in direction of force without force multiplication. It sits stationary, and while it doesn’t provide a mechanical advantage, its predominant value lies in convenience. Movable pulleys, on the other hand, offer a significant mechanical advantage by effectively halving the force required to lift a load, making them indispensable in several industrial applications including construction cranes and warehouse lifting machinery.
For complex operations, compound pulley systems combine fixed and movable pulleys. These systems offer superior mechanical advantage, making them perfect for heavy lifting tasks where load balancing is critical. An in-depth knowledge of how to configure these systems can significantly optimize performance and ensure safety.
Expertise in pulley operation goes beyond the understanding of types. It requires meticulous planning and execution. Consideration of materials is a pertinent factor. Contemporary pulley systems often utilize advanced materials such as fortified synthetics and high-grade metals to withstand rigorous demands. Expert operators assess conditions like weight, resistance, friction, and environmental exposure to select appropriate materials, ensuring longevity and reliability.
pulley operation
Strategic maintenance forms a crucial component of proficient pulley operation. Regular inspections for signs of wear, corrosion, and misalignment are non-negotiables for ensuring system integrity. Experienced practitioners advocate for routine lubrication practices, as they significantly reduce friction and prevent premature wear, enhancing a pulley’s efficiency and lifespan.
Safety cannot be overemphasized in the realm of pulley operations. Authoritative bodies like OSHA and ISO have laid down stringent guidelines ensuring that operatives are protected from the hazards associated with pulley systems. These include securing loads to prevent slippage, regular training for operators, and equipping workspaces with safety gear.
Trustworthiness in pulley operation doesn’t merely hinge on the physical act of using the pulleys but extends to the ethical adherence to safety and operational regulations. Professionals in the field must continually update themselves with the latest standards and practices, ensuring accountability and reliability in every lift.
Innovations in pulley technology are progressively altering conventional perspectives. Smart pulleys equipped with IoT sensors are now becoming mainstream, enabling real-time monitoring of load conditions and system parameters. This modern approach not only enhances operational efficiency but also sets new benchmarks in safety and precision.
Leveraging technology such as predictive analytics can further augment pulley system performance by anticipating maintenance needs and system upgrades before issues arise. Such proactive measures underscore the forward-thinking ethos required to excel in pulley operations today.
In conclusion, mastering pulley operations demands a blend of experience, expert knowledge, adherence to authoritative standards, and trust in processes and practices. By fostering expertise in these areas, you will not only optimize your pulley systems but also ensure they are effective, safe, and reliable. As pulleys continue to be integral to industrial operations worldwide, ongoing education and technological integration will remain pivotal in defining their role in future engineering innovations.