Rice mill pulleys, often an underappreciated component in the complex machinery used for processing paddy into rice, are crucial to the efficiency and functionality of rice mills. Understanding their role and significance can greatly enhance the performance of rice milling operations, a fact not always immediately apparent to those outside of the industry.
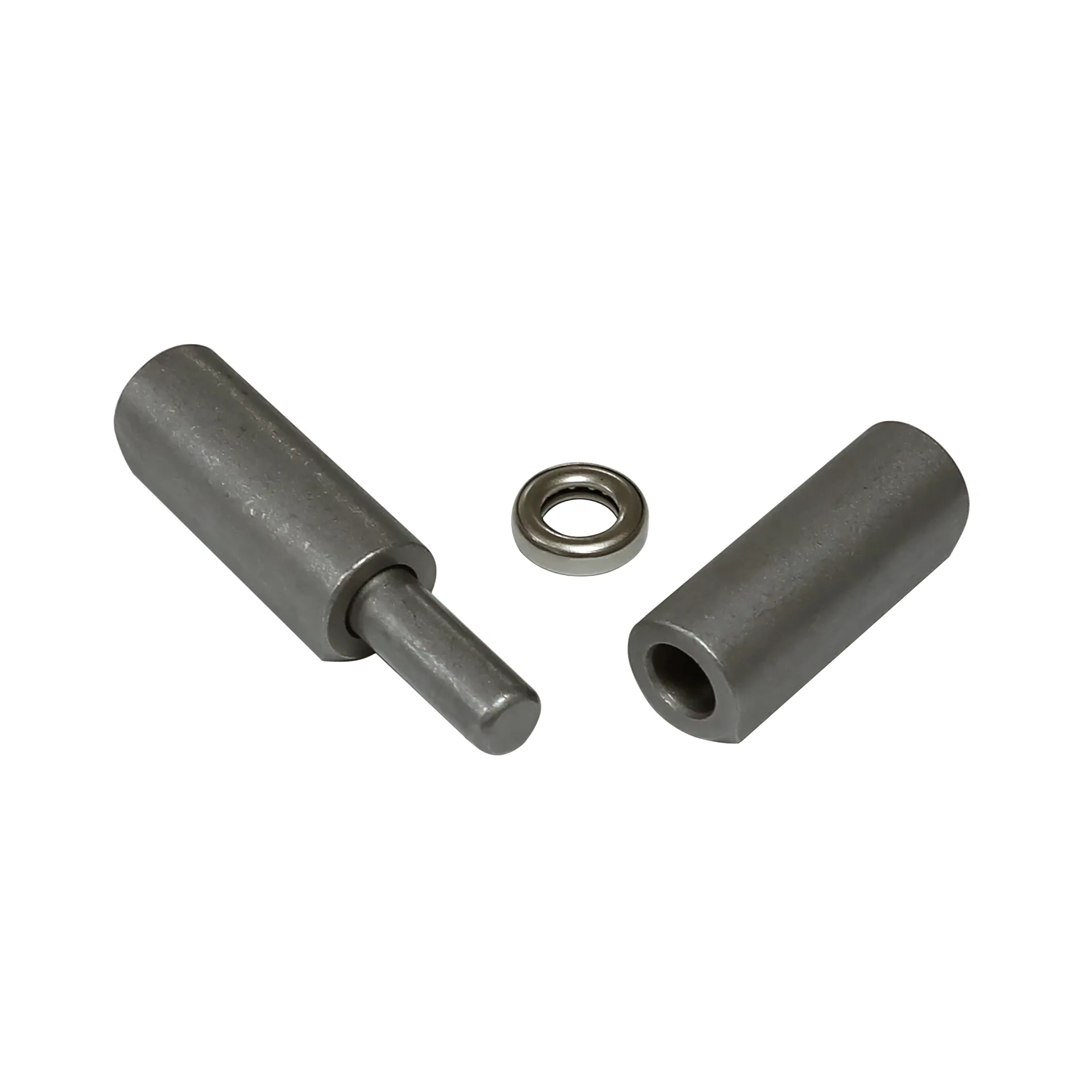
In the realm of rice milling, the pulley is a key element that transmits power from the mill's motor to its various operational parts. The choice of pulley – its size, material, and design – can significantly influence the operational efficiency and energy consumption of the mill. More importantly, the right pulley system ensures smooth functioning, minimizes downtime, and reduces maintenance costs, contributing to the overall profitability of rice milling businesses.
Traditionally, pulleys have been made from iron due to its strength and durability. However, advancements in materials science have introduced high-performance alloys and composite materials that offer greater longevity and resistance to wear and tear. These modern materials are transforming the rice milling industry by allowing for lighter, more efficient pulley systems that reduce the load on machinery and lower energy consumption. For example, pulleys made from cast nylon or steel alloys are known to offer superior performance in environments where friction and high-speed operation are prevalent.
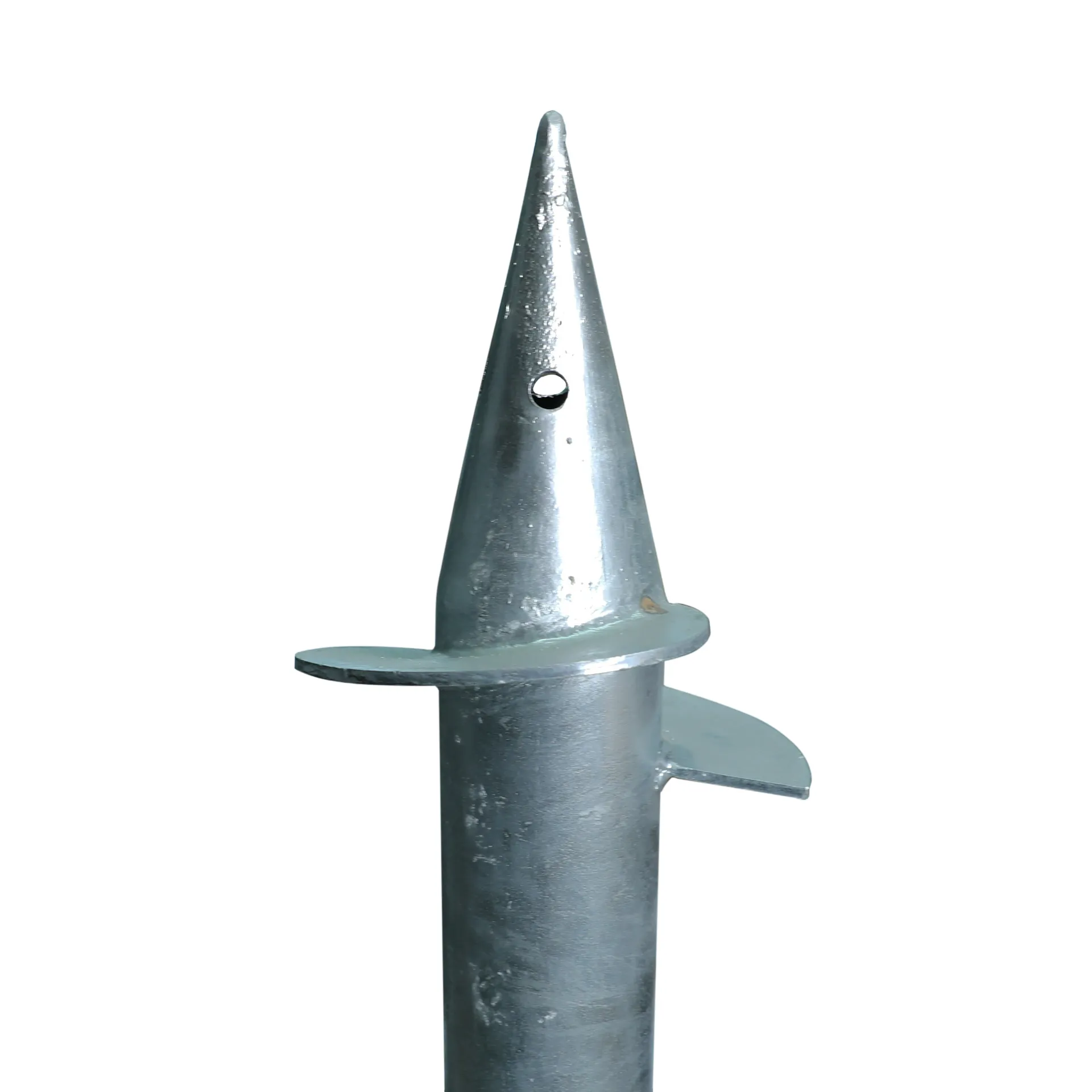
Expertise in the field of rice milling underscores the importance of precision in pulley design. The alignment and balance of pulleys must be meticulously calibrated to prevent operational inefficiencies such as belt slippage or undue strain on motors and other components. Engineers and technicians specializing in rice milling machinery are often required to undergo rigorous training to understand these dynamics fully. This specialization helps mills achieve peak operational efficiency, ensuring that the quality of rice processed remains consistently high.
rice mill pulley
Moreover, the authoritativeness of pulley specialist companies is reflected in their continuous investment in research and development. These organizations constantly work to innovate pulley designs that meet evolving industry demands, such as increased processing speed and reduced energy use. They often collaborate with universities and research institutes, conducting tests and experiments to advance materials technology and pulley design overall. Mills that adopt these state-of-the-art pulleys typically enjoy a competitive edge, with faster production rates and lower operational costs.
Trustworthiness in rice mill pulley products is often established through rigorous testing standards and certifications. Manufacturers adhering to ISO regulations and subjecting their products to stress and wear tests ensure that their pulleys can withstand the demanding environments of a rice mill. Such certifications provide rice mill operators with the confidence that their equipment will perform reliably over a long period.
A case in point is a rice mill in Southeast Asia that upgraded its outdated pulley system to a modern alternative crafted from advanced composite materials. This change resulted in a 20% reduction in energy consumption and a 30% increase in processing speed, demonstrating the potential impact of the right pulley choice on operational efficiency. The mill also reported a decrease in maintenance issues, further cementing the importance of investing in high-quality, trustworthy pulley systems.
In summary, while often overlooked, rice mill pulleys play a pivotal role in the efficiency and success of rice milling operations. Through a combination of material advancements, expert design, and authoritative manufacturing processes, these components ensure smoother operations, reduced costs, and increased productivity. As the industry continues to evolve, embracing cutting-edge pulley technologies will be crucial for mills seeking to maintain their competitiveness and sustainability in an increasingly demanding market.