In the fascinating world of mining, where every mechanism plays a vital role in ensuring the smooth operation of extracting valuable resources from the earth, the mining pulley stands out as one of the pivotal components. A mining pulley isn’t just a mundane piece of rotating machinery; it is a significant player that enhances efficiency and safety in mining operations.
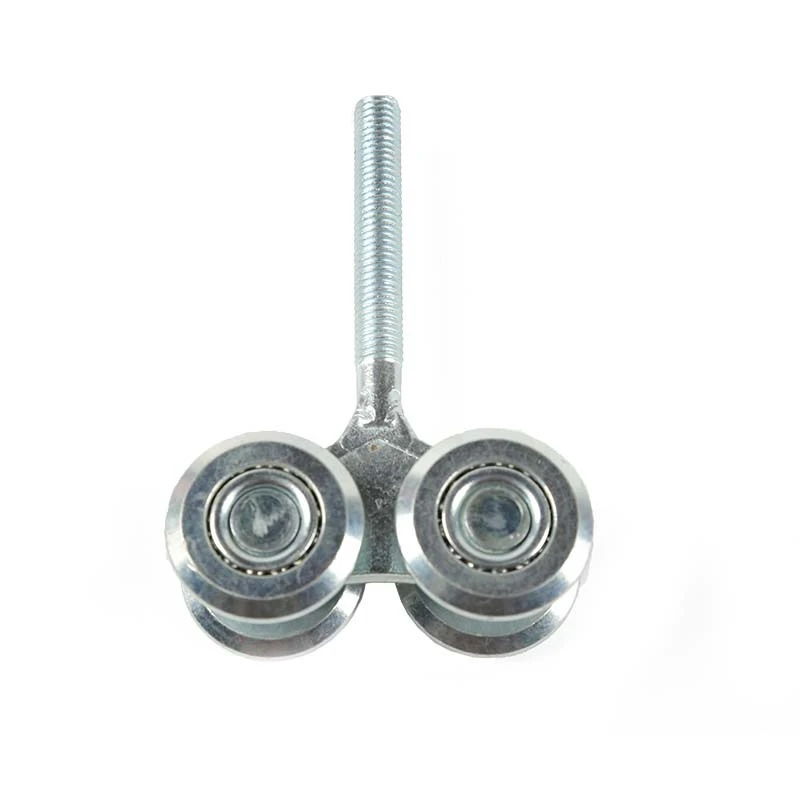
Mining pulleys are integral to conveyor systems, which are the veins through which mined materials flow from the extraction point to processing units. They are crafted from durable, wear-resistant materials designed to withstand the harshest conditions, including heavy loads and abrasive substances. The importance of the mining pulley in these conveyor systems cannot be overstated, making it an indispensable part of the mining domain.
One of the quintessential experiences that demonstrate the pivotal role of mining pulleys is observed in copper mines, where materials are often carried over significant distances from remote extraction sites. A seasoned mining engineer with over two decades of experience in the field recalls an instance in the Andean mines where a strategic choice of pulleys transformed productivity. By employing high-tension pulleys designed for elongated operational efficiency, they were able to reduce downtime and enhance the ore conveyance speed by 15%, an optimization that significantly bolstered the overall output.
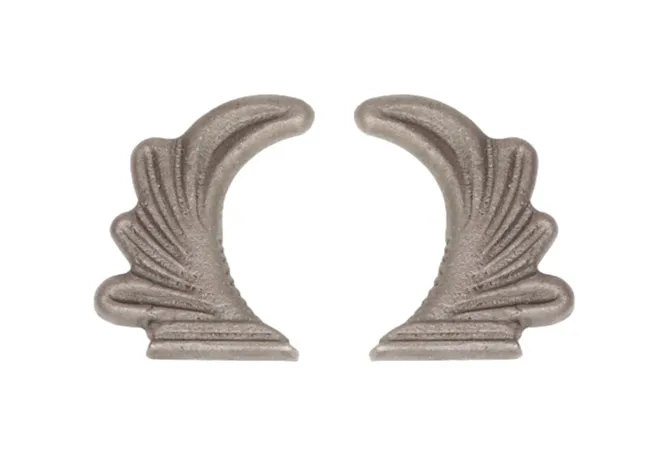
From an expertise standpoint, understanding the nuances of pulley design is crucial for mining operations. The two major types of mining pulleys, drive pulleys, and tail pulleys, each have distinct characteristics and functionalities. Drive pulleys are primarily responsible for the movement of the conveyor belt and are equipped with a higher torque capacity to drive the belt system efficiently. On the other hand, tail pulleys function as tensioning devices, ensuring the proper alignment and tension of the conveyor belt, thereby preventing slippage and potential operational downtimes.
mining pulley
Furthermore, the application of advanced materials and technology in manufacturing mining pulleys has paved the way for increased reliability and lifespan. Composite materials and alloys such as coated steel and aluminum composites have been proven to significantly reduce wear and tear while enhancing heat dissipation properties. When a mining operation in Western Australia adopted ceramic lagging on their drive pulleys, they saw a 40% reduction in maintenance costs over a year due to minimized wear and slippage, a testimony to the effectiveness of material innovation in mining pulleys.
As authoritative figures in the mining equipment manufacturing domain attest, the optimal selection and maintenance of mining pulleys is crucial not only for maximizing operational efficiency but also for ensuring safety. Properly maintained pulleys can prevent hazards such as conveyor belt failures and subsequent resource spillage, which can lead to costly shutdowns and environmental concerns.
Industry standards and regular inspections are emphasized to uphold safety and efficiency. For instance, a comprehensive review in a coal mine setting revealed that regular ultrasonic testing of pulley shafts could preemptively identify potential fractures, hence preventing catastrophic equipment failures.
Trustworthiness in the context of mining pulley usage also translates into the establishment of long-term partnerships with reputable pulley manufacturers. These manufacturers offer not just products but holistic solutions including installation, maintenance services, and emergency support. Certification of products according to international standards further assures the reliability and safety of these components in harsh mining environments.
Mining pulleys do not merely facilitate the movement of materials; they contribute significantly to cost-efficiency, safety, and the seamless operation of mining projects. Embracing innovations in pulley technology and adhering to stringent maintenance protocols can significantly elevate a mining enterprise’s competitive edge. By understanding and appreciating the sophisticated design and function of mining pulleys, mining operations can unlock enhanced productivity and ensure sustainable resource extraction for years to come. Whether approaching the complexities of pulley selection or optimizing their operational capacities, embracing a forward-thinking mindset with a deep respect for engineering precision establishes a pathway to success in the vast, challenging landscapes of mining.