Truck pulleys, an indispensable component in the heavy-duty vehicular landscape, have transformed in design and utility over the years, fulfilling critical roles in ensuring efficient operation and performance. Today, their significance in the automotive industry cannot be overstated. Drawing upon years of expertise and industry authority, understanding the nuances of truck pulleys can substantially enhance a vehicle’s operational lifespan and efficiency.
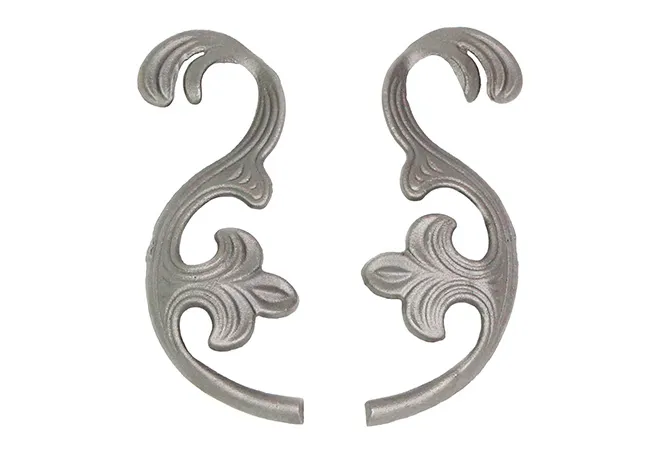
The essence of truck pulleys lies in their ability to transfer power within the truck's engine. They are shafts used to drive belts which in turn power various components such as the alternator, air conditioning compressor, and power steering pump. These devices are crucial in synchronizing with the engine's crankshaft to ensure that the energy generated is effectively distributed to necessary systems. The precision with which these pulleys operate is paramount for maintaining the efficiency and performance of any heavy-duty vehicle.
Expertise in truck pulleys requires a deep understanding of their types, materials, and the physics involved in their operations. Pulleys are typically classified into categories—flat belt, round belt,
and V-belt pulleys—each with its unique benefits. For instance, V-belt pulleys are widely recognized for their ability to carry higher load capacities due to their design, which increases friction and belt stability. This makes them particularly suitable for high-power applications prevalent in trucks.
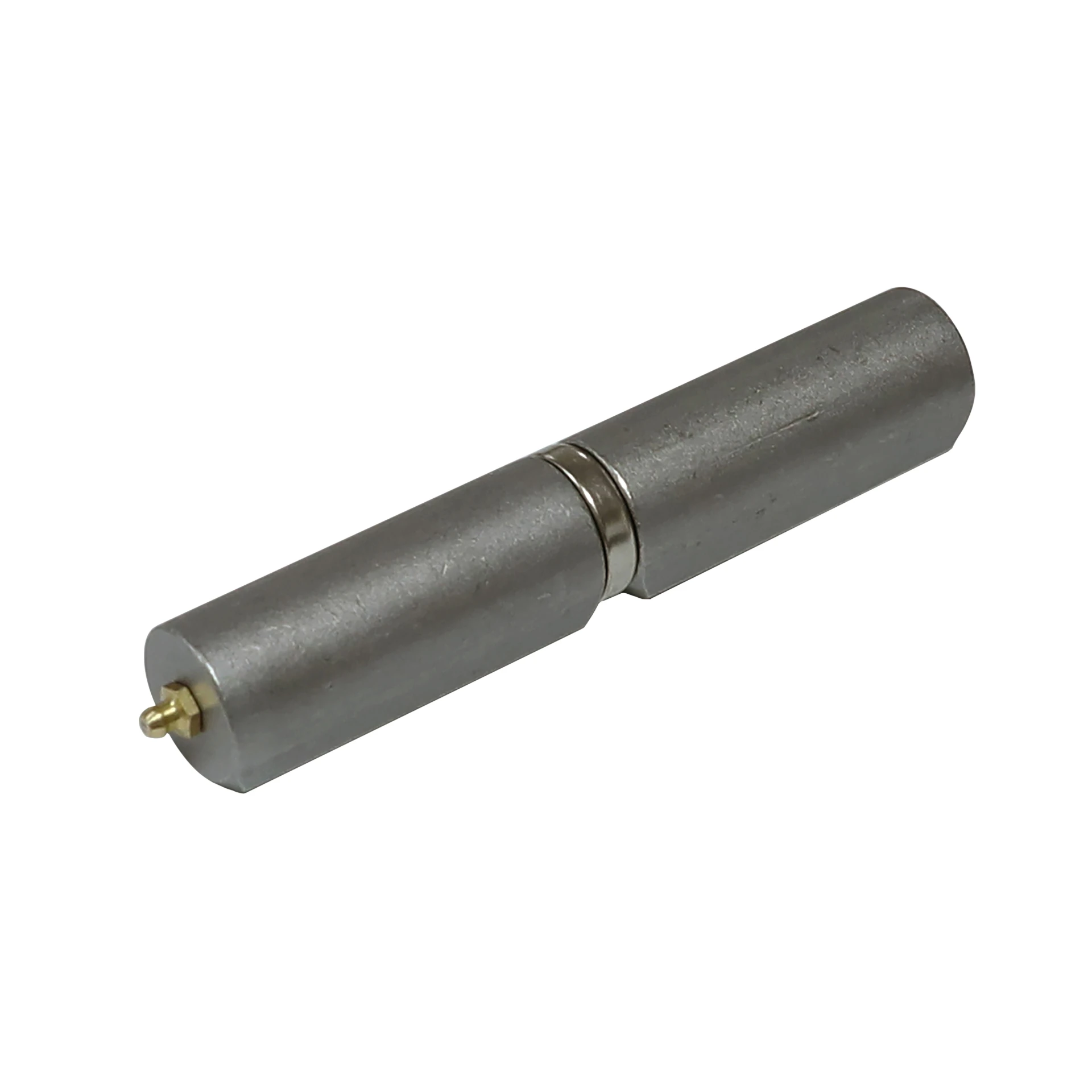
Material selection also plays a pivotal role in the efficacy of truck pulleys. Traditionally, pulleys have been constructed from metal alloys such as steel due to their durability and strength. However, modern innovations have led to the introduction of composite materials and specialized polymers. These materials offer the advantage of reduced weight without compromising on strength, which enhances fuel efficiency and decreases wear and tear on other engine components, thereby extending the vehicle's service life.
truck pulley
When considering the installation and maintenance of truck pulleys, professional insight reveals the necessity for precision alignment and tension control. Misaligned or improperly tensioned belts can result in suboptimal performance, causing increased engine wear or even system failure. Therefore, employing computerized alignment systems and using torque analytics can provide operators with accurate data ensuring that the truck pulley system remains in optimal condition, delivering consistent performance.
Acknowledged industry expertise in truck pulleys also highlights the recent advancements in predictive maintenance technologies. By incorporating sensors and IoT technologies, modern pulley systems can monitor real-time performance and notify operators of any deviations from normal patterns. This innovation not only augments the reliability of the truck pulley systems but also enhances trusting relationships with clients who are assured of their vehicles' dependability and reduced unscheduled downtimes.
Trustworthiness in the realm of truck pulleys can further be reinforced by partnerships with OEMs and relying on internationally recognized quality certifications. Pulleys produced with ISO or QS certifications provide an added layer of quality assurance that resonates with end-users and large fleet operators alike. This credibility is an invaluable asset in today's competitive automotive market.
In conclusion, a truck pulley is more than just a mechanical component; it is a linchpin that ensures the orchestral harmony of a truck’s multitude of systems. With the integration of advanced materials, precise alignment technologies, and predictive maintenance tools, their role continues to evolve. Understanding and leveraging these advancements fosters a deeper trust and reliance on truck pulleys, thus reinforcing their value in modern vehicular infrastructure. This knowledge is crucial for anyone involved in the automotive industry, from engineers and technicians to fleet managers looking to optimize vehicle performance and reliability.